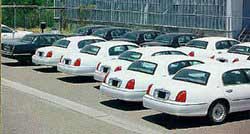
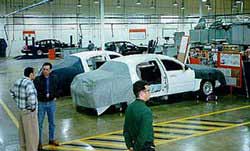
|
NEW CARS START THE
PROCESS
The factory always starts out with a new Lincoln
or Cadillac Coachbuilder Heavy Duty Package for
the Lincoln or Cadillac limousines. The factory uses New Lincoln,
Lincoln Navigator, Cadillac,
Cadillac Escalade, Hummer, Mercedes, Infiniti and Chrysler
300 new
cars to build the
New Limousines.
It is QVM and CMC Certified by Ford and General
Motors.
We can build custom
limousines on other cars as
well.
The factory enhances the OEM braking system to accommodate
the limo’s weight using oversized front brake
pads and rear braking cylinders. The factory uses each
model’s length and The factory selects the
appropriate Moog heavy-duty spring for a better
ride and greater safety. All units are fully
inspected prior to production. Then they are
stripped and covered, in and out, to protect the
body and interior. |
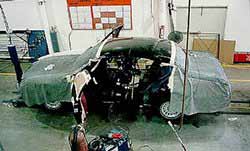
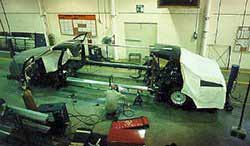 |
TOP QUALITY LASER GUIDED CUTTING SYSTEM
The
factory proprietary cutting unit.
Each vehicle from six to 120 inches is within
1/16-inch tolerance for exact specifications.
All body parts are locked in so there is no flex
to change our exact cut specifications. And, of
course, all specifications are equal to or above
QVM and CMC standards.
|
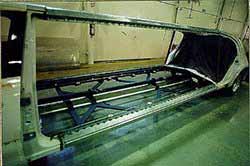
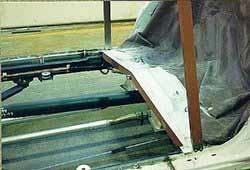
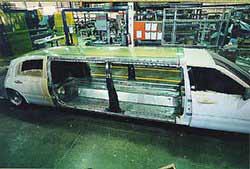
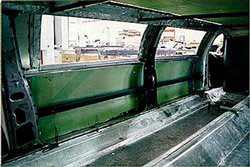
|
THE
CONVERSION
The factory uses only OEM body mounts for all
the
extensions, adding eight to every stretch from
85 to 120 inches. They strengthen the chassis,
smooth, and quite the ride. The factory’s
aluminized steel exhaust is mounted to improve
clearance. Heavy-duty isolators limit vibration.
Floor assembly is reinforced and prepared for
flat rear floor entrance area. This protects the
carpet from high heel tears and supports the
seating area. The factory uses OEM connectors to extend
the electrical body harnesses, then loom them to
protect from incision, humidity and temperature
extremes. The proprietary cross-member frame
design delivers unequaled crash performance. The
OEM brackets, connectors, and double-wall,
stainless steel chassis, fuel, and brake line
extensions give backbone to the OEM extended
150,000-mile warranty. The factory assembles the drive
shaft extension from OEM materials, then unit
balance each other for a vibration free ride.
The
factory’s low-alloy, high-strength floor, rocker
panel and header extensions are two-sided,
hot-dipped, galvanized steel exceeding OEM
standards. They resist damage even in the
fiercest weather. Only factory pillars are used
in all the extensions and are built to exact QVM
standards.
All interior panels are then primer etched for
rust protection prior to installation of the
side panels. For passenger protection, The
factory weld
eight-gauge rectangular tubing to the front,
center and rear OEM pillars in all 120-inch
models and to the front and rear pillars in all
other models. Then, The factory adds structural foam
adhesive for rigidity. |
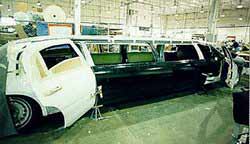
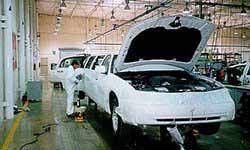
|
ALL REFINISHING IS DONE AT EYE LEVEL
The
exterior seven-step, epoxy-urethane coating
is unique to the factory in the limo industry.
It’s resistant to acid rain damage and chipping,
while retaining a gloss high enough to dazzle
any eye. |
 |
ROOF AND SIDEWALL
The factory roof bracing system bonds
high-strength hot galvanized steel on 16-inch
centers to the existing roof panel. The result
is a vastly stronger roof for better client
safety and operator piece of mind. Our side
panel extensions are veritable works of art.
They’re bolted, not The welded, to the car, making
them easy to replace in the event of collision.
To reduce weight and eliminate rust the factory uses a
combination of aerospace composites,
high-strength marine alloy aluminum, stainless
steel fasteners, and non-conductive sealants.
For our roof and side wall insulation The
factory use
double-radiant-barrier aluminized Mylar,
expanded closed-cell polyurethane foam. |
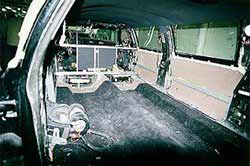 |
TOP QUALITY AIR CONDITIONING AND AIR EVAPORATING
The
two air conditioning evaporators are built of
30-finned, aluminum/copper tubing to dissipate
heat rapidly without rust. Each provides 19,200
BTUs of cooling capacity at face level. The
heater core produces volumes of warm air, which
The factory funnel to floor level, where it rises.
Heat-blistered pavement is no match for Our
factory’s floor pan insulation. The
energy-absorbing material of OEM-style wool felt
drowns out sound, vibration, and temperature
extremes. This construction exceeds federal
safety standards. The factory use the same materials plus
a radiant barrier below our evaporators to
enhance heating and cooling. The auxiliary air
conditioning condenser and eleven-inch cooling
fan improves heat exchange.
|
|
DIVIDER ASSEMBLY
For the divider assembly the factory uses only
high-strength aluminum extrusion OEM lift
mechanisms for trouble-free operation year after
year. Service personnel will find work easier
and faster with our electric system control
panel from ICS or Mastercon. Low-voltage
switching signals are reliable and safe—and
carry a limited lifetime warranty. The panel
itself is mounted on the passenger side of the
divider. |
|
UPHOLSTERY AND SEATS
Nothing seems to age a limousine more than
sagging or worn seats. The factory anticipates
and counteracts this prolonged usage with
tubular steel, eleven-gauge tension springs,
Ricarro-style webbing, and multiple density
foams. |
|
RESERVE STARTING BATTERY
The MVPU1 battery is a sealed lead acid
high-output workhorse. The auxiliary air
conditioning condenser and eleven-inch cooling
fan improves heat exchange. The OEM heavy-gauge
vinyl top won’t fade or peel for years. Our
auxiliary air conditioning condenser improves
heat exchange. |
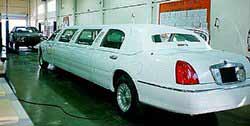
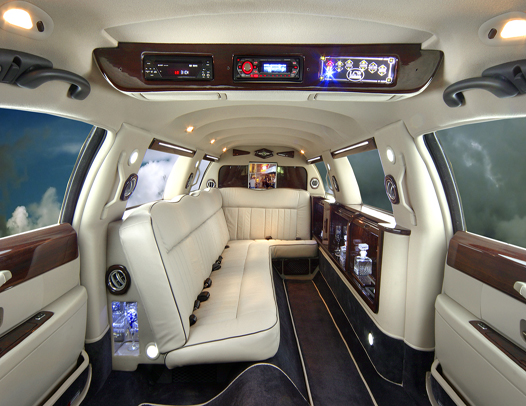 |
FINAL INSPECTION: INTERIOR, EXTERIOR
This completes the build process for a superior
limousine:
YOUR NEW LIMOUSINE! |
|
|